Plaza-i Logistics & Inventory
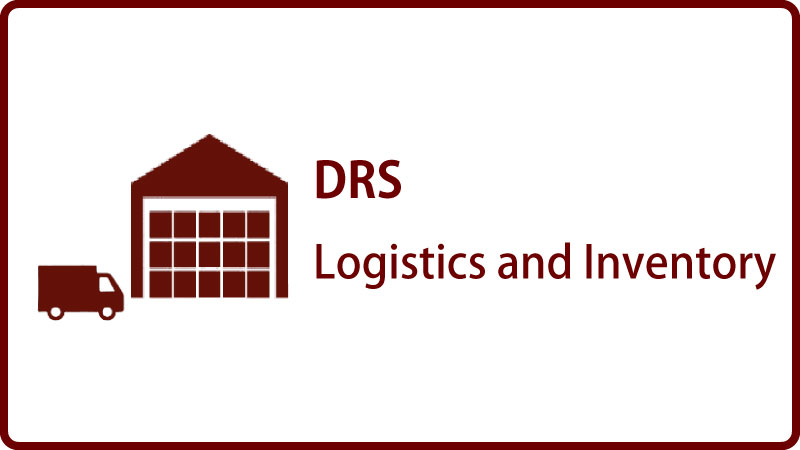
Plaza-i Logistics and Inventory(Distribution Requirement and Inventory Control)
Handles stock-in/out process, stock-in/out schedule management, reservation of car allocation, distribution arrangement, and physical inventory taking.
Overview
・This module consists of two systems: one is logistics management, which is used by warehouse staff who handles actual receiving and shipping of goods based on stock-in/out instructions issued by Sales or Purchase Management module, and the other is inventory management, which covers accounting inventory transactions, physical inventory taking, inventory valuation, and inventory reports.
・Depending on your business, you can use well-made logistics functions, or use high quality inventory management functions, or both. We recommend using it together with Plaza-i Sales Management module (SOE).
Solving these issues (features)
・Using Plaza-i at your company warehouse or an entrusted warehouse, you can smoothly carry out shipping instructions, picking and packing items, and delivery note output.
・Stock-in/out processes will be performed based on instructions by sales or purchase in-charge personnel, reducing the quantity variance between book and physical inventory.
・Tracking your company’s inventories held by other companies in the same way with other companies’ inventories stored in your company such as consignment, rental, after delivery before inspection, and holding for repair, you can reduce a burden of physical inventory taking.
・Thanks to inventory allocation and management by such status as Defect and Before Inspection, you can check items available for delivery on a real-time basis.
Main menu + Screen image
This module consists of two systems: one is logistics management, which is used by warehouse staff who handles actual receiving and shipping of goods based on stock-in/out instruction issued by Sales or Purchase Management module, and the other is inventory management, which covers accounting inventory transactions, physical inventory taking, inventory valuation, and inventory reports.
・Stock-in/out Request
・Transaction Request
・Stock-in/out Schedule (Picking List, Stock-in/out Schedule List)
・Inventory Inquiry – By Item, By Warehouse
・Car Allocation, Car Allocation Status Inquiry, Distribution Arrangement
・Stock-in/out Confirmation
・Inventory Transaction Entry
・Physical Inventory Taking
・Inventory Valuation (Inventory Monthly Update)
・Inventory Report
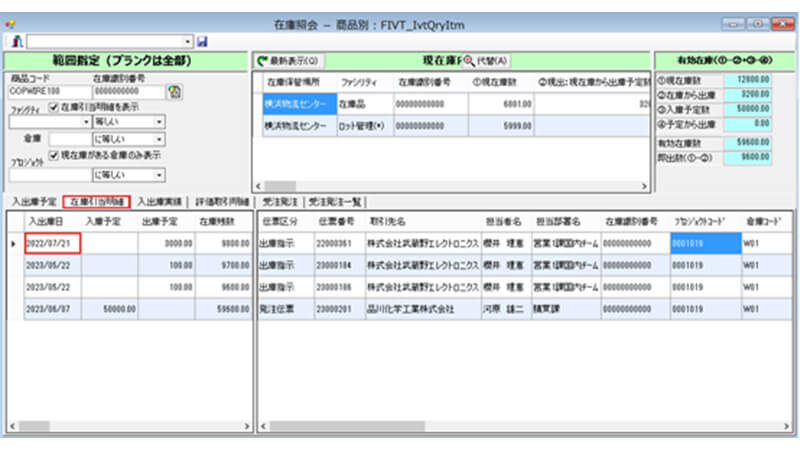
Detailed features
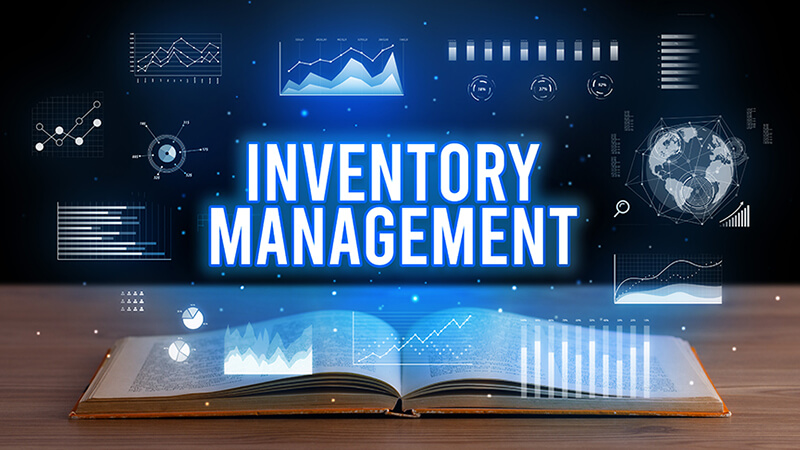
Useful "Facility" Function
In addition to By Item Code, Place, and Lot/Serial Number, inventory is managed by Facility (management status) which is one of the characteristics of this Plaza-i module.
To be specific, inventory items can be freely categorized by service level by setting such facilities as rental items, trade items to be shipped, used items, items currently being inspected, in-transit items, items approved to be returned (RMA), and items to be scrapped. Also, manage your own assets (e.g., rental goods) separately from other company's assets (e.g., items deposited for repair). By making use of the Facility status, you need only one inventory inquiry screen to keep track of how many rental goods or items deposited for repair are stored in which warehouse.
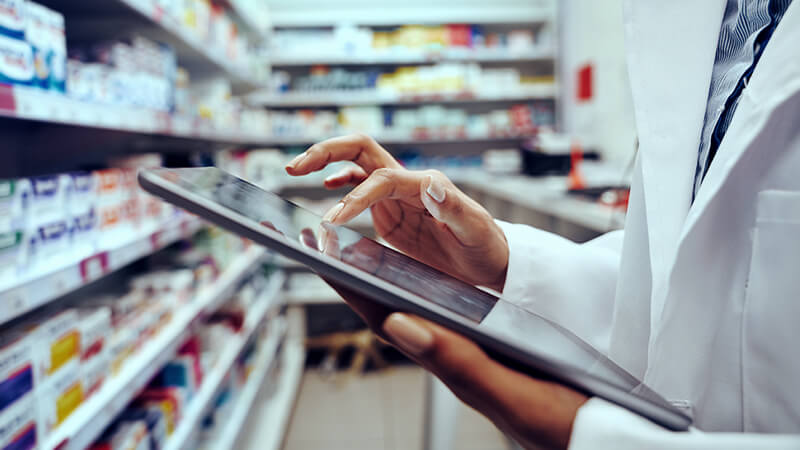
Inventory Reports
You can output an inventory list or see it on the screen, which shows quantities, unit prices, and amounts of previous month, current month stock-in, current month stock-out, month end balance for stock items of all facilities.
Since this inventory data is the accounting data, which can be reconciled against inventory controlling account in trial balance, you can output the list of the past months at any time.
The inventory report, which shows warehouses and facilities horizontally, is very useful for companies who have a lot of warehouses, or inventory locations.
Various slow-moving item reports are available depending on the nature of the items. For instance, for standard stock items, slow-moving items will be simply determined to check whether or not the rotation rate is lower than the specified rate. For OEM item purchases, slow-moving items will be determined by checking stock items which are purchased before a specified period. And for lot management items, they will be determined by aging based on expiration date or receiving date.
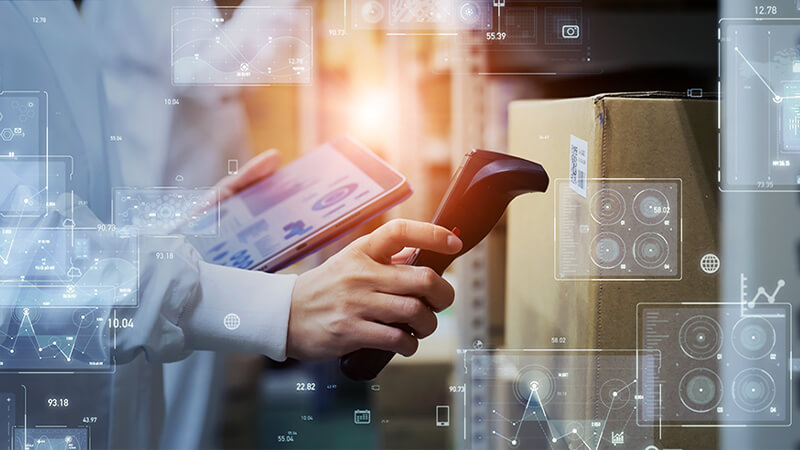
Inventory Inquiry is Useful for Sales Representatives
This module can tell you where and how many of a specific item exists and who reserved it by which voucher in real time.
Inventory Inquiry – By Warehouse shows you, for example, a list of inventories rented to clients nationwide by serial number.
Sales representatives can check details of receiving schedules. Therefore, they can offer enhanced services to their customers such as provision of delivery information or timely response for sales orders.
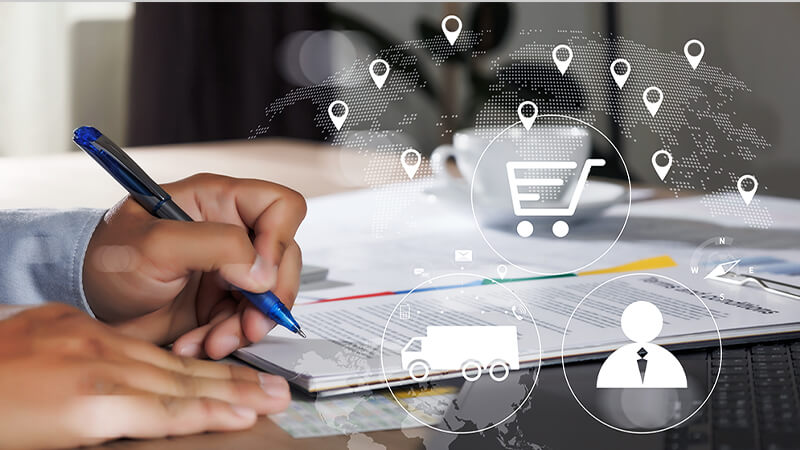
Various Inventory Valuation Methods
Plaza-i handles various inventory valuation methods such as standard cost, monthly average, moving average, first-in-first-out, individual, and last purchase cost methods.
As for the standard cost method, the standard unit price revision menu is prepared, which allows you to create transactions to record differences due to standard unit price revision.
The monthly average method is available not only per item but also per warehouse and per facility, which eliminates the influence of inventory transfers. Shipping unit price will be evaluated as well as month-end unit price, so that cost of sales will also be updated. Furthermore, the lower of cost or market method at year-end is supported.
The moving average method adopts calculation of shipping unit prices per transaction, and if there are any mistakes, you can process Reversal and Correction Voucher Creation to correct them.
As for the first-in-first-out method, shipping unit prices will be calculated every time you execute stock-in/out confirmation.
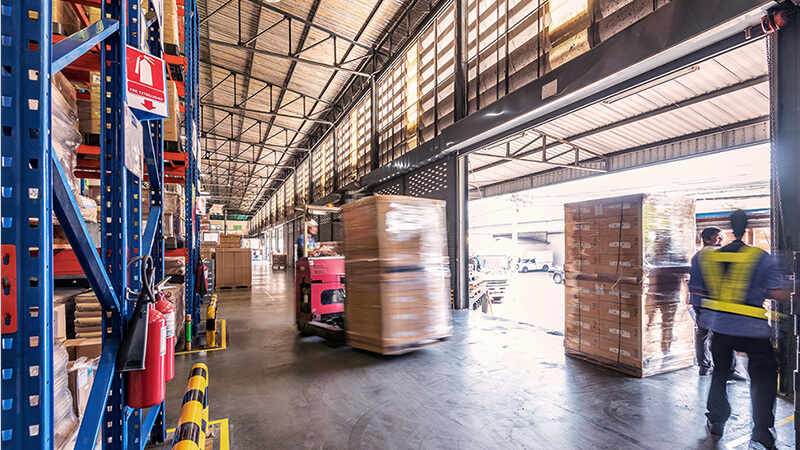
Physical Inventory Taking
・Perform physical inventory taking by using the physical inventory taking preparation list or physical inventory tags, and input inventory tags.
・Then, the system will summarize physical inventory tags by item and compare it with book balance.
・If there are any variances, you can investigate the reasons, and then enter sales or purchase vouchers if necessary.
・ Final variances will be recorded on the physical inventory taking entry screen by location.
・Physical inventory taking is available both in real time and in the past. If you execute it in real time, you can prohibit any entries for future dates by creating inventory taking plan.
・Finally, you can output physical inventory taking difference report, hand it to the person in charge, and after it is approved, execute physical inventory taking confirmation, and then create accounting transactions. As a result of physical inventory taking confirmation, any entries of differences on that day for that location will be prohibited.